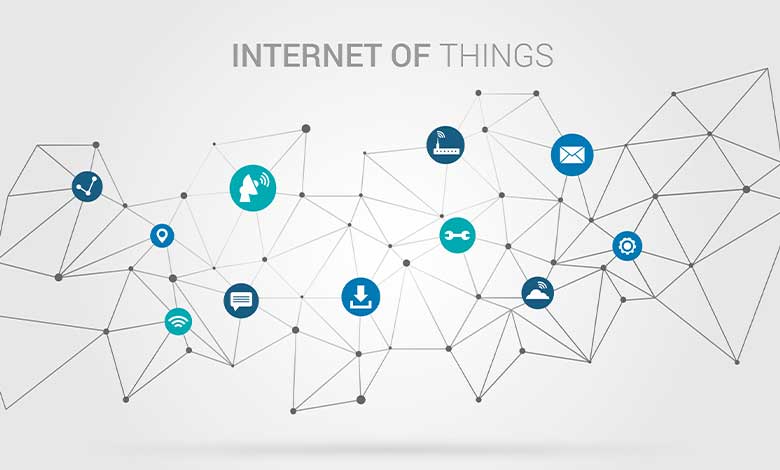
Cloud and edge computing have allowed internet-connected appliances to create and permeate many industries. From smart home devices to the factory floor, the Internet of Things encompasses a myriad of application fields. Industrial process automation with the use of cloud computing gave birth to a new definition of IoT, the Industrial Internet of Things (IIoT).
Computers, sensors and embedded systems were used in manufacturing and plants long before a certain Coke vending machine became the first internet-connected device. Ever since then device connectivity and interoperability has sky-rocketed. In today’s rapidly changing world, almost 40 years later, industrial equipment and machinery manufacturers have been banking on digitization at sclae to drive digital transformation and optimize their business in the era of Industry 4.0.
Smart IT’s own experience in building a Business Process Management Software around information gathered from factory floor sensors prompted it to look at how construction and manufacturing have implemented IIOT to address business needs. Another case involving the building of a CRM-like system that unified data from many different softwares used by a construction company, MyTrusted Builder, prompted us to look at how software could key in solving some of the associated risks of digitizing manufacturing.
How does IIOT benefit manufacturing?
The first proper uses of IIoT in manufacturing were recorded in 2002, when the cloud allowed for hardware and goods to upload crucial metrics and data onto the internet and exchange it between systems. Effectively this did not entirely mark the end of Distributed Computer Systems, which were used for decades before hardware could connect to the internet.
Some of the major uses of IIoT are:
Inventory management
One of the first use cases for IIoT became asset tracking. Manufactured goods were packaged and tagged with codes or RFID markers that allowed scanners and sensors to relay their whereabouts. This benefited buyers and suppliers by allowing both to use an interface or dashboard to monitor the goods across different stages of the supply chain. In some instances it even allowed for the global tracking of manufactured goods and offered a convenient way to manage risks, avoid gaps and ensure reliable monitoring on every step of the way.
Predictive maintenance
Much of the industrial equipment and hardware used in manufacturing and hardware these days is able to run diagnostics on the equipment it is installed on. This valuable data, when aggregated and analyzed, can shine a light on system critical maintenance way in advance of any major failure. Hence, by reducing the risk of downtime, through preventive and predictive maintenance, the equipment can be mended at the most convenient time, without the business losing money.
Industrial process automation
Much like with inventory management, tracking processes, just like goods and equipment, can zoom in opportunities to elevate production efficiency. Programmed processes can give insights to peak load and output, which allows businesses to further optimize their processes and plan to either scale or improve current use of machinery and other hardware. The work between multiple departments or branches can be further polished by reducing communication interval, wherein different equipment can “speak” to each other through a common platform.
Electrical distribution
Machinery is notorious for the vast consumption of electrical energy and such resource-heavy industries run up a significant bill very fast. By narrowing down the times when equipment is actually used at any given point in the production process, operators can control when this or that equipment can be shut down to save on energy costs. Besides focusing on renewable and alternative sources of energy, forward-thinking industries can reduce overheads in what was otherwise known as a necessary evil (spend more to produce more).
Analytics and optimization
Many industries have been relying on purchasing analytics to optimize in-house processes, all the while ignoring their own data-gathering potential. Cloud or edge connected devices can process volumes of data to provide a more refined sneak peek at performance. Organizations that give time and attention to analysis of their own data can do much in the way of optimizing internal processes to eliminate unnecessary costs, save time, and have more control over all stages production. Data Science is a hot topic in the business world as more and more businesses leverage Big Data to identify pain points and ensure growth.
Application fields
The earliest adopters of automation were the automotive and oil and gas industries. It should come as no surprise that such industries with “a lot of moving parts” would make the foray into a centralized management system. Robotic Process Automation and interconnected devices has allowed to blend the human and machine workforce into an efficient synergy and guarantee the most productive results.
Safety, connectivity and analytics have been the major points on the radar of the oil and gas industry. Connected devices have been able to relay crucial data points that have allowed to gather information from the device ecosystem. This results in reduced negative impact on the environment and provides awareness of threat-prone systems, such as pipes and boring stations.
There is vast untapped potential in the development IIoT in relation to other industries as well. This chiefly applies to agriculture and mining, industries that have not received fluctuating levels of attention across the globe when it comes to automation. In the age of population growth and growing concern for the well-being of individuals, agriculture, mining and even medicine production could further benefit from the introduction of internet-connected devices.
Obstacles and what lies ahead
With the connection to the internet the most obvious and perhaps the biggest threat that appears to connected systems is security. Cyber-criminals have been known to infect and paralyze smart devices, exploiting them to their ends. Such threats greatly impede the adoption of these benevolent technologies at scale across many industries. However, software based architectures are said to benefit security and prevent intrusions, as well as deter data leaks and the unwanted sharing of sensitive information.
According to McKinsey, a data-market strategy according could incentivize more industries to onboard the cloud and tap into its wealth of processing power.
When it comes to advancing your business, whatever the scale, companies like McKinsey recommends to build an ecosystem of business and technology partners to tackle the implementation of an IIoT platform. It is true that without the right solution providers digital transformation will be next to impossible to implement. The company’s article also suggests that such transformations do not have to come at a great cost to businesses.
Pavel manages content marketing and PR at Smart IT, alongside a team of talented software engineers with a background in competitive programming. Smart IT is a Belarus-USA based IT outsourcing services and software development company engaged in helping clients across the globe with on-demand services and solutions.