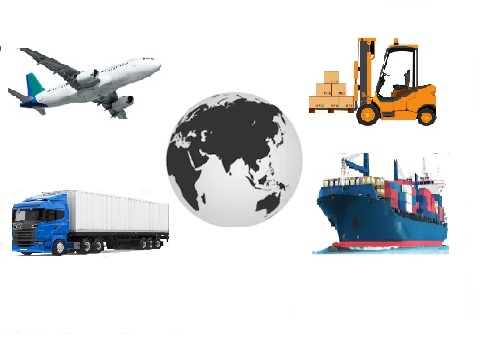
Enhancing resilience and agility of Supply Chain amidst a global pandemic: A Cloud ERP approach.
Milan Chowdhury
Background: Impact of an unprecedented global pandemic on existing supply chain of any organization is a known fact today. Be it global or local, supply chain disruptions crippled thousands of manufacturers and their trade partners equally in uncertain times of COVID-19. Majority of supply-side disruptions were caused by restrictions imposed in cross-border logistics & transportation activities and additional precautions needed to be taken to restrict corona transmission – resulting severe delay in raw materials and semi-finished goods delivery to manufacturers which in turn impacted finished goods production. Interestingly, majority of demand-side disruptions happened due to a different reason: under-stocking and overstocking driven by lack of inventory visibility and poor collaboration amongst supply chain partners. Definitely, end consumer sentiments played a role in this disruption and demand-pull initiated from there only. But unfortunately, this artificial demand-pull got further amplified by supply chain partners (typically retailer, wholesaler, distributor, manufacturer and supplier) when it moved upwards creating a typical supply chain phenomenon known as Bullwhip Effect (BWE).
A bullwhip effect (BWE, shown in Fig-1) refers to a phenomenon where unexpected fluctuations, variations and distortions in demand is observed within a supply chain as a result of shift in end customer demand. This distortion propagates upwards (from customer to manufacturer to supplier) in an amplified manner and cripples demand forecasting accuracy of entire supply chain – resulting in inventory disruptions, poor quality, higher cost and low customer satisfaction. The bullwhip effect was named after the whip used for bulls – when a bullwhip is cracked, a small wrist movement makes a successively larger wave moving along the length of the whip. Behavioral causes (ex: consumer sentiments) are often attributed to start a bullwhip effect. Minor variance in demand can create panic among the supply chain partners. In absence of a formal communication channel they tend to lose confidence and multiply the variance by ordering manifold of actual demand. Thus, sharing information using a common platform across entire supply chain can play a vital role to mitigate bullwhip effect. Imagine if upstream supply chain partners have access to view the actual demand and inventory levels of downstream partners, the numbers will never be amplified so significantly. For example, if retailers can have the visibility and transparency of their manufacturers’ inventory level, then they will not include safety stock and buffer in their ordering quantities. All these can be achieved by collaboration (sharing information using a common platform) amongst the partners across entire supply chain.
Fig.-1: Demand amplification due to Bullwhip Effect
Many of the FMCG retailers based out of eastern India, I had a chance to interact with at the time of COVID-19 lockdown period complained that even when government is allowing them to stock and sell consumer goods customers are asking for, unfortunately not available with wholesalers or distributors. Which is why once the product becomes available, they are going for higher ordering quantity as they don’t have any clear stock visibility of wholesalers or distributors. Thus, even if wholesalers hoard the product for personal profit, no retailer will ever have a clear visibility. This is a classic starting point of a typical Bullwhip effect where every supply chain partner tend to lose confidence on other and further disrupt the supply chain by over ordering or under ordering
Possible Solution: As already highlighted, sharing information using a common platform across entire supply chain can play a vital role to mitigate bullwhip effect. Imagine if upstream supply chain partners have access to view the actual demand and inventory levels of downstream partners, the numbers will never be amplified so significantly. For example, if retailers can have the visibility and transparency of their manufacturers’ inventory level, then they will not include safety stock and buffer in their ordering quantities. All these can be achieved by collaboration (sharing information using a common platform) amongst the partners across entire supply chain. Technology can play a major role to tame bullwhip effect across supply chain enabling reliable communication and collaboration amongst supply chain partners.
How can cloud help? As we know, cloud computing is an emerging area of information and communication technology (ICT) where service provided by network of remote servers hosted on the internet to store, manage and process data, instead of local server or personal computer. Cloud computing services are cheaper, maintenance-free and flexible for end customer as they are ‘on-demand’ in nature and charged on ‘pay-as-you-use’ model. Small businesses (for example, retailers in a supply chain), who have a very low Capex capability can purchase cloud services at low cost. Enterprise Resource Planning software hosted by cloud technology is termed as “Cloud ERP Software”. Most cloud service platforms are constructed utilizing virtualization and burden adjusting innovation that enables applications to be conveyed over numerous servers and database resources. This is why cloud ERPs have recently become the most cost effective dependable way to collaborate with supply chain partners. This paper is considering the rollout of cloud ERPs across supply chain as a first step to digital-supply-chain-transformation where cloud based ERP platforms can be used by all supply chain partners to collaborate and share information along supply chain with lowest possible cost. A typical solution here could be a Manufacturer’s on-premise Central ERP connected with ERP Cloud platform of supply chain partners (ex: retailer, wholesaler, distributor, manufacturer and supplier) who can collaborate with limited inventory visibility of immediate next sc-partner (Fig-2). A small application in a retailer’s smartphone can be used as collaboration tool. As cloud ERP services are ‘on-demand’, billed on ‘pay-as-you-use’ model and offers seamless mobility, all supply chain partners can use it to collaborate with each other with least possible cost to mitigate the impact of Bullwhip effect along entire supply chain as a first step towards digitizing supply chain in post COVID-19 world. This technology based collaboration will definitely enhance resilience and agility of any supply chain amidst global pandemics like COVID-19 and mitigate supply chain disruptions in uncertain times.
Fig.-2: Proposed Architecture for collaborating supply chain partners with cloud-ERP
Experimental Implementation: As a part of experimental implementation to demonstrate capability of cloud ERP platforms as a systematic tool for information sharing and collaboration amongst supply chain partners in order to mitigate BWE of entire supply chain a simulation set up was arranged. To replicate a real supply chain (consisting of retailer, wholesaler, distributor, manufacturer and supplier) experiencing bullwhip effect, we have taken help of Beer Distribution Game (1960) set up in an experimental way (Fig.-3). Five volunteers acting as supply chain entities passed demand information upstream with a piece of paper (with numbers written on it) and inventory chips to immediate downstream player to fulfill demand and replenish stock. This way customer demand and product moved through the supply chain without any verbal communication between the partners. There was one shipping delay box in between two partners and objective of each partner was to meet the customer demand without excess inventory or shortage. Obviously, customer demands were pre-determined but not revealed to anyone except the retailer and revealed at regular intervals as the game progresses. Thus, each partner had to decide on ordering quantities based on locally available information. Each partner had to keep in mind a few factors while deciding on ordering quantities. Those include: existing demand, expected demand, current inventory, incoming inventory-in-transit and desired inventory. Each partner tried to reduce the gap between desired and current inventory keeping in mind inventory-in-transits. Therefore, following basic rule was adhered to while ordering:
Orders to be Placed (at time T) = Backlog (of T-1) + Current Orders (at time T).
If a partner was having enough inventory, he had to ship all the orders to ship and record new inventory.
If a partner was not having enough inventory, he had to ship whatever inventory he had and record the remaining unfilled orders to fill as new backlog. A record sheet was used to record each of the individual partner’s Inventory, Backlog and Order Placed quantities. After a few rounds of play, the ordering patterns of SC partners started to exhibit demand amplification (BWE) as per the equation suggested by Chen et al. (2000):
BWE = Var(Q) / Var(D)
Where, Var(Q) is variance of retailer orders and Var(D) is variance of customer demand.
Idea was to conduct two experiments, record and graphically represent ordered quantities for each to investigate any mitigation in BWE. In first beer game experiment, partners are restricted to any communication except order information pass. In second beer game experiment, partners are allowed to communicate with a cloud based group chat application to update inventory, backlog and order figures after each movement. The detailed experiment has been elaborated in the research paper [9] in Reference section.
Fig.-3: Beer Game set up with partners’ position and ordering information flow
Key Takeaways: Order behavior graphs drawn (Fig.-4) from record sheets of Experiment-1 (without collaboration) Vs. Experiment-2 (with collaboration) showed that BWE amplification ratio at peak has reduced from 1.85 to 1.20 showing mitigation of demand amplification across supply chain in second experiment – due to systematic information sharing and collaboration amongst SC partners (through cloud based group chat application). This demonstration of mitigation (of BWE) was based on a Beer Game simulation experiment setup and a cloud based group chat application was used as a basic collaboration platform. More accuracy and complex business objectives can be achieved by using advanced cloud ERP platforms.
Fig.-4: Order behavior comparison charts Experiment-1 Vs. Experiment-2
The untapped opportunity in post-COVID19 world: “Embrace Digital” is going to be the keyword for post-COVID19 supply chain world. Digital supply chain transformations will ensure lowest possible manual intervention, accurate visibility of inventory, paperless transactions, ordering automation and AI enabled demand forecasting to reduce disruptions. Furthermore, in order to enhance resilience and agility of supply chain, collaboration of supply chain partners will always play a major role. Cloud ERPs have the potential to become an effective tool of collaboration with least possible cost, lowest complexity and high availability. This is why Cloud ERPs can help to promote a collaborative-trade-ecosystem which will be key for survival in post COVID19 world.
I expect this article has provided basic insights and opened new opportunities for future research in the area of supply chain collaboration with cloud ERPs. This article may also open up new product development opportunity for cloud ERP software manufacturers and developers, who want to tap this low-cost niche market segment for small scale businesses. As more complex business objectives can be achieved with complex algorithms, entrepreneurs interested to setup their tech startups can take a note of this future business model and work further to make this reality. In my opinion, Saas (Software-as-a-service) products of existing cloud ERP vendors are still costly and unaffordable for many small and medium businesses who will be needing to collaborate with their supply chain partners in order to ensure business continuation in post COVID19 era. Here lies the untapped opportunity for relatively new vendors who can develop Android-based smartphone applications and connect them with cloud ERPs via internet.
References:
[1] Forrester, J.W. Industrial Dynamics- Systems Dynamics Series, Productivity Press, MIT Press, 1961. [2] Sterman, J.D. “Modeling managerial behavior: misperceptions of feedback in a dynamic decision making experiment”, Management Science, 1989. [3] Towill, D.R. and Naim, M. “Supply chain: partnership sourcing smoothens supply chain dynamics”, Purchasing & SupplyManagement, 1993.
[4] Lee, H.L., Padmanabhan, V. and Whang “Information distortion in a supply chain: the bullwhip effect”, ManagementScience, 1997. [5] Scavo, F., Newton, B. & Longwell, M. 2012. Choosing between cloud and hosted ERP, and why it matters. Computer Economics Report. Vol. 34 No. 8. [6] Arnesen, S., ‘Is a Cloud ERP Solution Right for You?’, Strategic Finance. 2013 [7] Zadeh, A.H., Akinyemi, B. A., Jeyaraj A. & Zolbanin, H. M., Cloud ERP Systems for Small and-Medium Enterprises: A Case Study in the Food Industry. Journal of Cases on Information Technology, October-December 2018. [8] Chen, F. Drezner, Z. Ryan, J.K. Smith-Levi, D. Quantifying the bullwhip effect in a simple supply chain: The impact of forecasting, lead times and information. Management Science. 2000. [9] Chowdhury, Milan. Mitigating the Bullwhip Effect in Supply Chain: A Cloud computing approach. RESEARCH REVIEW International Journal of Multidisciplinary. Feb 2019. url: https://rrjournals.com/past-issue/mitigating-the-bullwhip-effect-in-supply-chain-a-cloud-computing-approach-2/